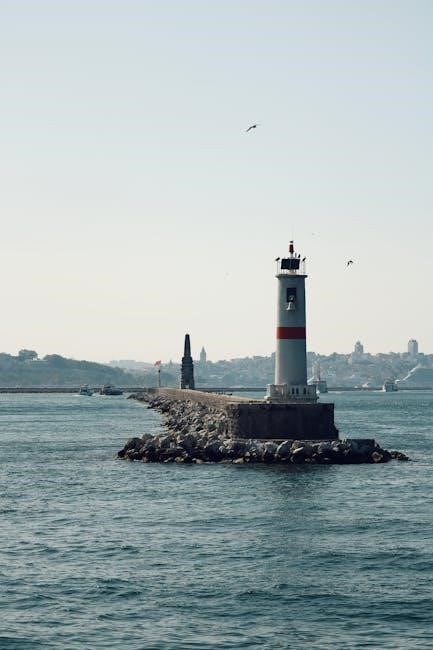
mig wire size guide
Selecting the right MIG welding wire size is crucial for achieving optimal weld quality and efficiency. This guide provides essential insights into wire sizes, types, and applications, ensuring proper material penetration and aesthetics for various projects.
Importance of Selecting the Right MIG Wire Size
Selecting the correct MIG wire size is vital for ensuring proper weld penetration, strength, and aesthetics. Using the wrong size can lead to lack of fusion, excessive spatter, or insufficient weld depth. The right wire diameter ensures efficient material flow, optimal arc stability, and minimal waste. Proper wire selection also enhances welding speed and reduces the risk of defects, making it a critical factor in achieving high-quality, durable welds for any project.
Overview of MIG Welding Wire Types
MIG welding wires vary in type and composition, catering to different materials and applications. Common types include ER70S-6 for steel, flux core wires for outdoor use, and specialty wires for alloys like stainless steel or aluminum. Each wire type offers unique properties, such as improved penetration, corrosion resistance, or adaptability to dirty conditions, ensuring versatility for various welding needs and material requirements.
Understanding MIG Welding Basics
MIG welding uses a continuous wire electrode and shielding gas to create clean, strong welds. Ideal for various metals, it offers versatility and efficiency in welding processes.
What is MIG Welding?
MIG (Metal Inert Gas) welding is a process that uses a continuous wire electrode and inert shielding gas to join metals. It’s known for clean, strong welds and works on various materials like steel, aluminum, and stainless steel. The wire is fed through a welding gun, creating an electric arc that melts the wire and base material, forming a weld. This method is efficient and widely used in automotive, industrial, and home projects.
Key Components of MIG Welding
MIG welding involves a power source, wire feeder, welding gun, shielding gas, and workpiece. The power source generates current; the wire feeder delivers the wire at a set speed. The gun holds the wire and gas nozzle, while shielding gas protects the arc. The workpiece is the material being welded. Together, these components ensure clean, precise welds, making MIG welding versatile for various applications.
Factors Influencing MIG Wire Size Selection
Material thickness, welding position, desired penetration, and aesthetics are key factors in selecting the appropriate MIG wire size for optimal results in various welding applications.
Material Thickness and Its Impact
Material thickness is a critical factor in selecting the appropriate MIG wire size. Thicker materials require larger wire diameters to ensure sufficient penetration and strength, while thinner materials need smaller wires to prevent burn-through and maintain precision. Proper wire size selection ensures optimal weld quality, avoiding defects and maintaining structural integrity across various applications.
Welding Position and Technique
Welding position and technique significantly influence wire size selection. Flat position welding allows for consistent feed rates, while vertical or overhead welding may require adjustments to maintain control. The angle and manipulation of the MIG gun affect weld pool dynamics, impacting penetration and aesthetics. Proper technique ensures efficient material fusion, regardless of position, optimizing both weld quality and appearance across various applications.
Desired Weld Penetration and Aesthetics
Desired weld penetration and aesthetics play a crucial role in selecting the appropriate MIG wire size. Thicker wires typically achieve deeper penetration, ensuring strong joints, while thinner wires provide better control over weld appearance. The choice of wire size and type directly impacts the visual appeal and structural integrity of the weld, making it essential to balance functionality with the desired cosmetic outcome for professional results.
MIG Wire Size Chart and Recommendations
A MIG wire size chart is essential for selecting the correct wire diameter and type based on material thickness, ensuring optimal weld quality and performance.
Standard Wire Sizes for Common Materials
Selecting the right wire size is crucial for achieving strong, clean welds. For steel, common wire diameters range from 0.8mm to 1.2mm, with 0.9mm being ideal for thin materials like 1.6mm sheet metal. Aluminum welding often uses 0.9mm or 1.0mm wires to ensure proper fusion. Stainless steel typically uses 0.9mm or 1.0mm wires for corrosion resistance. Always consult a wire size chart to match the wire diameter to your material thickness for optimal results and durability.
Adjusting Wire Size for Different Material Thicknesses
Material thickness dictates the appropriate MIG wire size; Thinner materials (1;6mm) often use 0.8mm or 0.9mm wires to prevent burn-through. Thicker materials (above 4mm) require 1.2mm wires for deeper penetration. Adjusting wire size ensures proper fusion without compromising material integrity or aesthetics. Always refer to a wire size chart for precise recommendations based on your specific project requirements to achieve professional-grade welds consistently.
MIG Wire Types and Their Applications
MIG welding wires vary in type, each suited for specific tasks. ER70S-6 is ideal for general steel welding, while flux core wires excel in outdoor, dirty conditions. Specialty wires cater to unique alloys, ensuring optimal performance across diverse welding scenarios.
ER70S-6 Wire for General-Purpose Welding
ER70S-6 is a versatile MIG welding wire designed for general-purpose steel welding. It offers excellent mechanical properties, including high strength and low spatter. Suitable for both thin and thick materials, it provides consistent weld penetration and aesthetics. Ideal for automotive repairs, fabrication, and construction, ER70S-6 is a reliable choice for achieving high-quality welds in various applications.
Flux Core Wire for Outdoor and Dirty Conditions
Flux core wire is ideal for welding in outdoor or dirty environments due to its self-shielding properties. It eliminates the need for external shielding gas, making it perfect for fieldwork. Available in various sizes, flux core wire offers strong penetration and is resistant to porosity. Its durability and ease of use make it a preferred choice for construction and repair projects where clean conditions are not feasible.
Specialty Wires for Specific Alloys
Specialty MIG wires are designed for welding specific alloys like stainless steel, aluminum, and nickel. These wires are formulated to match the base metal’s properties, ensuring compatibility and corrosion resistance. They come in various sizes to suit different project requirements. Using the correct specialty wire ensures strong, durable welds with minimal risk of defects, making them essential for industries requiring high-performance materials. Proper selection enhances both the structural integrity and aesthetic appeal of the weld.
Material Thickness Guidelines
Material thickness determines the appropriate MIG wire size. Thinner materials require smaller diameters for precise control, while thicker materials need larger wires for deeper penetration and strength. Proper matching ensures optimal weld quality and prevents defects.
Thin Materials: 0;8mm vs. 0.9mm Wire
For thin materials, choosing between 0.8mm and 0.9mm MIG wire is critical. The 0.8mm wire is ideal for very thin sheets, offering precise control and minimal heat input, reducing warping risks. Conversely, 0.9mm wire provides slightly better penetration and is often recommended for materials like 1.6mm steel, balancing strength and aesthetics. Both sizes are suitable for automotive and hobby projects, but 0.9mm is preferred for its versatility in thin-section welding applications.
Thicker Materials: 1.0mm and Above
For thicker materials, MIG welding wires with diameters of 1.0mm and above are recommended. These larger wires provide greater penetration and strength, making them ideal for industrial and heavy-duty applications. They are commonly used in construction and manufacturing where thicker steel or alloy materials are involved. The 1.0mm wire strikes a balance between penetration and aesthetics, ensuring robust welds without excessive heat input. Shielding gases like 75% Argon/25% CO2 enhance performance. Always adjust welding parameters for optimal results with thicker wires.
Shielding Gas Considerations
Shielding gases protect the arc and molten weld from atmospheric impurities, ensuring clean, high-quality welds. They influence arc stability, penetration, and weld appearance, optimizing wire performance.
How Shielding Gas Affects Wire Performance
Shielding gas composition significantly impacts MIG wire performance by influencing arc stability, penetration depth, and weld quality. Different gas mixes, such as argon or CO2 blends, optimize the arc for specific wire types. Proper gas flow prevents atmospheric contamination, ensuring clean welds. Incorrect gas selection or flow rate can lead to porosity or lack of fusion, highlighting the importance of matching gas type to wire and material requirements for optimal results.
Gasless vs. Gas-Shielded MIG Welding
Gasless MIG welding uses flux core wire, eliminating the need for external shielding gas, making it ideal for outdoor or dirty conditions. Gas-shielded MIG welding relies on inert gases like argon or CO2 to protect the arc, offering cleaner welds with less spatter. The choice depends on the environment and desired weld quality, as gasless setups are more versatile but may produce more slag, requiring additional cleanup compared to gas-shielded methods.
Welding Current and Voltage Settings
Proper current and voltage settings are essential for optimal MIG welding performance. Matching the wire size to the current ensures consistent arc characteristics, while adjusting voltage controls the arc’s intensity and penetration. Correct settings prevent overheating or insufficient fusion, ensuring high-quality welds. Always refer to the manufacturer’s guidelines for specific wire and material combinations to achieve the best results.
Matching Wire Size to Welding Current
Wire size directly influences welding current requirements. Thinner wires, like 0.8mm or 0.9mm, operate effectively at lower currents, typically between 50-150 amps, to prevent overheating. Thicker wires, such as 1.2mm or 1.6mm, require higher currents (150-300 amps) for proper fusion and penetration. Correctly matching wire size to current ensures consistent arc stability and avoids issues like lack of penetration or excessive spatter. Always consult a wire size chart or manufacturer guidelines for precise settings.
Adjusting Voltage for Optimal Arc Characteristics
Adjusting voltage is crucial for optimal arc characteristics in MIG welding. The right voltage ensures a stable arc, proper penetration, and minimizes spatter. If the voltage is too low, the arc may be weak, leading to insufficient fusion. Too high, and it can cause overheating or excessive spatter. Fine-tuning the voltage based on wire size and material thickness is essential for achieving consistent, high-quality welds. Always refer to manufacturer guidelines for specific voltage recommendations.
Common Applications of MIG Welding
MIG welding is widely used in automotive repairs, industrial manufacturing, and home projects due to its efficiency and versatility in joining various materials effectively.
Automotive Repairs and Fabrication
MIG welding is integral to automotive repairs and fabrication, offering high-speed, clean joints for steel and aluminum components. Its versatility is ideal for repairing body panels, exhaust systems, and frames.
The process ensures minimal distortion, making it perfect for restoring vehicle structural integrity. Fabricators rely on MIG welding for creating custom parts, such as roll cages or chassis components, due to its precision and strength.
Industrial Manufacturing and Construction
MIG welding is widely used in industrial manufacturing and construction for its efficiency and scalability. It excels in joining thick steel and aluminum components, making it ideal for frameworks, machinery, and large-scale structures. The ability to use different wire sizes ensures proper penetration and strength for heavy-duty applications. In high-volume production, MIG welding’s speed and reliability make it a cornerstone of industrial workflows, ensuring consistent and durable results.
Home and Hobby Projects
MIG welding is a versatile choice for home and hobby projects, offering ease of use and adaptability. For thin materials like 1.6mm sheet metal, 0.9mm wire is often recommended over 0.8mm due to better performance and consistency. This ensures clean, precise welds for tasks such as repairing appliances, fabricating furniture, or creating decorative items. The right wire size enhances both functionality and aesthetics, making MIG welding a favorite among DIY enthusiasts and small-scale fabricators.
Troubleshooting Common Issues
Common MIG welding issues include wire feeding problems and porosity. Proper wire size selection and shielding gas usage help resolve these, ensuring smooth and defect-free welds consistently.
Wire Feeding Problems and Solutions
Wire feeding issues often arise from incorrect wire size, liner misalignment, or debris buildup. Regularly clean the feed system, ensure proper wire tension, and use the correct drive rolls. Using a wire size chart can help prevent these problems, ensuring smooth operation. Proper storage and handling of the wire also reduce feeding issues, promoting consistent weld quality and efficiency in MIG welding processes.
Porosity and Lack of Penetration Issues
Porosity and insufficient penetration are common issues in MIG welding, often due to incorrect wire size, improper shielding gas flow, or inadequate heat input. Adjusting the wire size and ensuring sufficient voltage can improve penetration. Cleanliness of the base material is critical to prevent porosity. Using the right gas type and flow rate also enhances weld quality, reducing defects and ensuring strong, durable joints in various welding applications.
Best Practices for MIG Welding
Proper storage and handling of MIG wires prevent contamination. Regular maintenance of equipment ensures smooth operation. Always match wire size to material thickness for optimal results and durability.
Proper Wire Storage and Handling
Store MIG welding wire in a cool, dry place to prevent moisture absorption. Keep the wire spool sealed when not in use to maintain quality. Handle the wire gently to avoid kinking or tangling, which can disrupt feeding. Always clean the wire before use to remove dirt or oil. Proper storage and handling ensure consistent weld quality and prevent issues during the welding process.
Maintenance of MIG Welding Equipment
Regular maintenance of MIG welding equipment is essential for optimal performance. Clean the welding gun and torch regularly to remove splatter and debris. Lubricate moving parts to ensure smooth wire feeding. Replace worn-out contact tips and nozzles promptly. Check and replace the shielding gas hoses if damaged. Proper upkeep prevents equipment malfunction, ensures consistent wire feeding, and prolongs the life of your MIG welder, leading to better weld quality and reduced downtime.
Comparison with TIG Welding
MIG welding offers faster speeds and versatility, especially for thicker materials, while TIG welding provides precision and aesthetic results, often preferred for thinner materials and high-quality finishes.
Wire Size vs. Tungsten Electrode Size
MIG welding wire size and TIG welding tungsten electrode size serve different purposes. MIG wire size determines material penetration and weld strength, while TIG electrodes focus on arc stability and precision. Thicker MIG wires suit heavier materials, whereas smaller tungsten electrodes are ideal for thin, intricate welds. Both tools require careful selection to match the specific welding task and material thickness for optimal results.
Choosing Between MIG and TIG for Specific Tasks
Selecting MIG or TIG welding depends on the task’s requirements. MIG welding excels in speed and efficiency for thicker materials and general-purpose jobs. TIG welding, with its precise control, is better suited for thin materials, complex geometries, and high-quality, aesthetically pleasing welds. Consider factors like material thickness, desired finish, and production speed when deciding between the two processes for optimal results in automotive, industrial, or hobby projects.
Selecting the right MIG wire size is crucial for optimal welding results. Consider material thickness, equipment settings, and desired outcomes. Proper techniques ensure strong, clean welds every time.
Choosing the right MIG wire size is vital for optimal weld quality. Material thickness, shielding gas, and welding technique influence wire selection. Thinner materials (0.8mm-1.0mm) require smaller diameters, while thicker materials need larger wires. Shielding gas type (active or inert) affects arc stability and penetration. Proper wire size ensures adequate fusion, prevents porosity, and enhances aesthetics. Always match wire size to current and voltage settings for consistent results across various applications.
Final Tips for Optimal MIG Welding Results
Always store MIG wire in a dry, clean environment to prevent moisture absorption. Use the correct drive rolls for your wire type to ensure smooth feeding. Maintain consistent welding techniques and adjust settings based on material thickness. Regularly clean and maintain equipment to prevent issues like porosity or lack of penetration. Proper wire handling and storage are key to achieving professional-grade welds in any project.